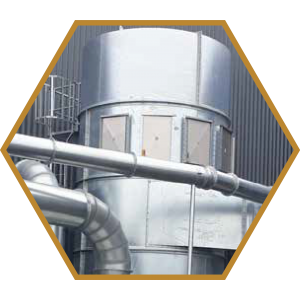
VIGIFLAP
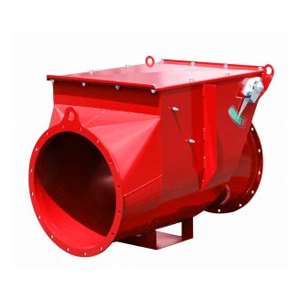
APPLICATIONS
The VigiFLAP is a non-return valve designed to prevent overpressure or flame caused by a downstream explosion (dust collectors, filters, cyclones…) to propagate in the piping system.
The valve is held open by a lever arm. It can be used both at the entrance and at the exit of the filter. This allows to isolate the filter from an explosion or an overpressure.
In case of explosion, the valve closes and remains locked preventing the progress of the flame. The unlocking of the flap is done manually.
Explosion Isolation valve
HIGH CERTIFICATION TEST
To get our Atex certificate (N° INERIS 19ATEX0016X) according to the standard EN16447: 2014, we carried out our explosion tests in the most extreme conditions and as close as possible to the reality of the use of the product, with for example:
- Protected Zone Pipeline :
All test carried out with a pipeline after the flap (picture1). - Flap locked open:
Automatic release of the valve by the pressure of the explosion - Floating flap:
During the test the flap valve is held fully open until the appropriate
time of release. - Vent panel on test vessel:
No open ports were used during test but vent panels were always used.
SOON:
In few months our VIGIFLAP certificate will be improved with the following additionnal features Atex certified :
- Size until diameter 1370mm
- ST3
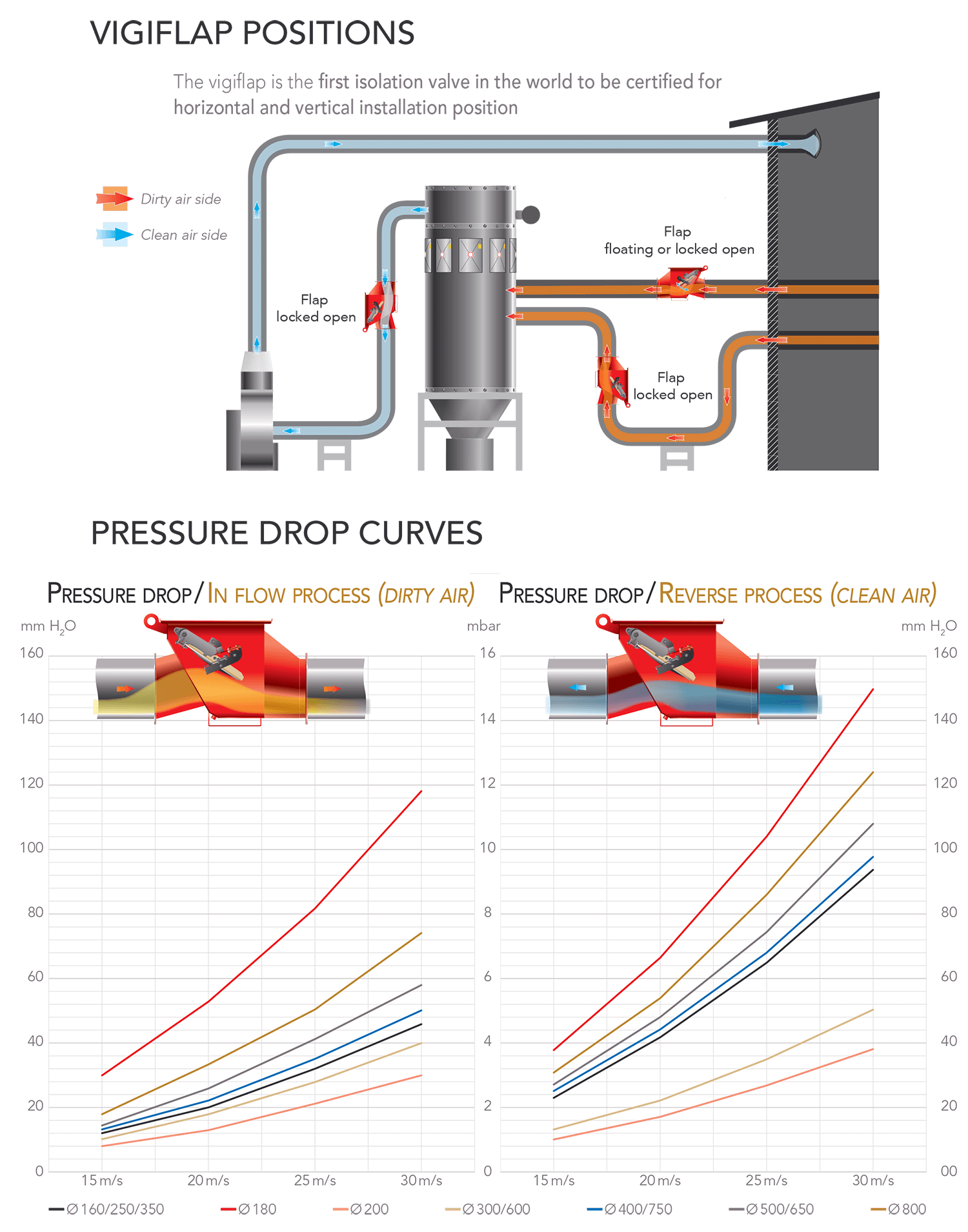
DN (mm) | DN (inch) | Minimum Vessel Volume | LMin* Min Mounting Distance | LMin** Min Mounting Distance | L Max Max Mounting Distance | |
---|---|---|---|---|---|---|
DN (mm) | DN (inch) | Minimum Vessel Volume | LMin* Min Mounting Distance | LMin** Min Mounting Distance | L Max Max Mounting Distance | |
DN (mm) | DN (inch) | Minimum Vessel Volume | LMin* Min Mounting Distance | LMin** Min Mounting Distance | L Max Max Mounting Distance | |
DN (mm) | DN (inch) | Minimum Vessel Volume | LMin* Min Mounting Distance | LMin** Min Mounting Distance | L Max Max Mounting Distance | |
DN (mm) | DN (inch) | Minimum Vessel Volume | LMin* Min Mounting Distance | LMin** Min Mounting Distance | L Max Max Mounting Distance | |
ø160 | ø6* | 0,70m3 | 4,0m | 6,0m | 17m | |
ø160 | ø6* | 1,35m3 | 3,0m | 5,0m | 17m | |
ø180 | ø7* | 0,70m3 | 4,0m | 6,0m | 17m | |
ø180 | ø7* | 1,35m3 | 3,0m | 5,0m | 17m | |
ø200 | ø8* | 1,35m3 | 4,6m | 6,6m | 17m | |
ø250 | ø10* | 1,35m3 | 4,0m | 6,0m | 17m | |
ø300 | ø12* | 2,90m3 | 4,6m | 6,6m | 17m | |
ø350 | ø14* | 2,90m3 | 4,2m | 6,2m | 17m | |
ø400 | ø16* | 4,50m3 | 5,2m | 7,2m | 17m | |
ø450 | ø18* | 4,50m3 | 4,7m | 6,7m | 17m | |
ø500 | ø20* | 6,05m3 | 5,8m | 7,8m | 17m | |
ø550 | ø22* | 6,05m3 | 5,5m | 7,5m | 17m | |
ø600 | ø24* | 7,65m3 | 7,2m | 9,2m | 17m | |
ø650 | ø26* | 7,65m3 | 6,7m | 8,7m | 17m | |
ø700 | ø28* | 7,65m3 | 6,4m | 8,4m | 17m | |
ø750 | ø30* | 10,00m3 | 7,3m | 9,3m | 17m | |
ø800 | ø32* | 10,00m3 | 6,9m | 8,9m | 17m |
* Floating in horizontal position:
Flap valve activated by the working air flow
** Vertical position
With elbows
Flap valve kept open by its spring blade system
Kst max | ≤250 bar.m/s |
Kst min | 50 bar.m/s |
Pmax | 10bar 145psi |
Working | St1 St2* |
ATEX Marking | ![]() |
Pred max in protected vessel | ≤ 0.5 bar |
VIGIFLAP Resistance | 2.0 bar |
MIE | ≥ 10 mJ |
MIT | ≥ 400º C ≥ 752º F |
Atex Inside | Zone 20 (II 1D) |
MESG | 1,7mm 0.067 inch |
Dust range | All dusts (metal dust included) |
Air flow speed | 15m/s ≤ v ≤ 30m/s 3000 ≤ v ≤ 6000 ft/min |
Dust concentration | No Limit |
Air flow range | Pull flow |
*Vessel (potential explosion source)
**Organic dust, synthetic dust and metal dust
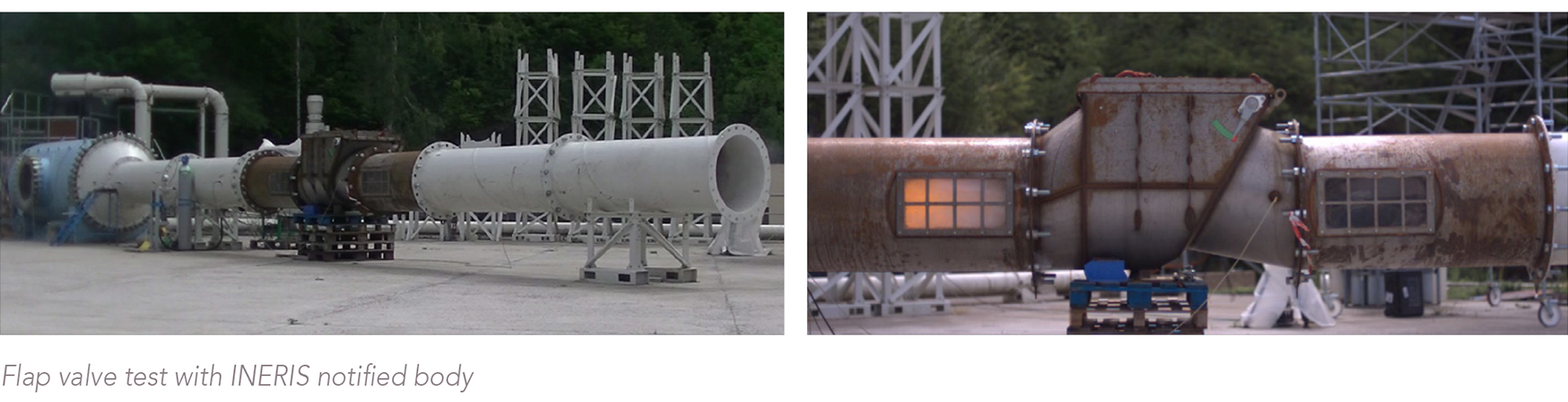
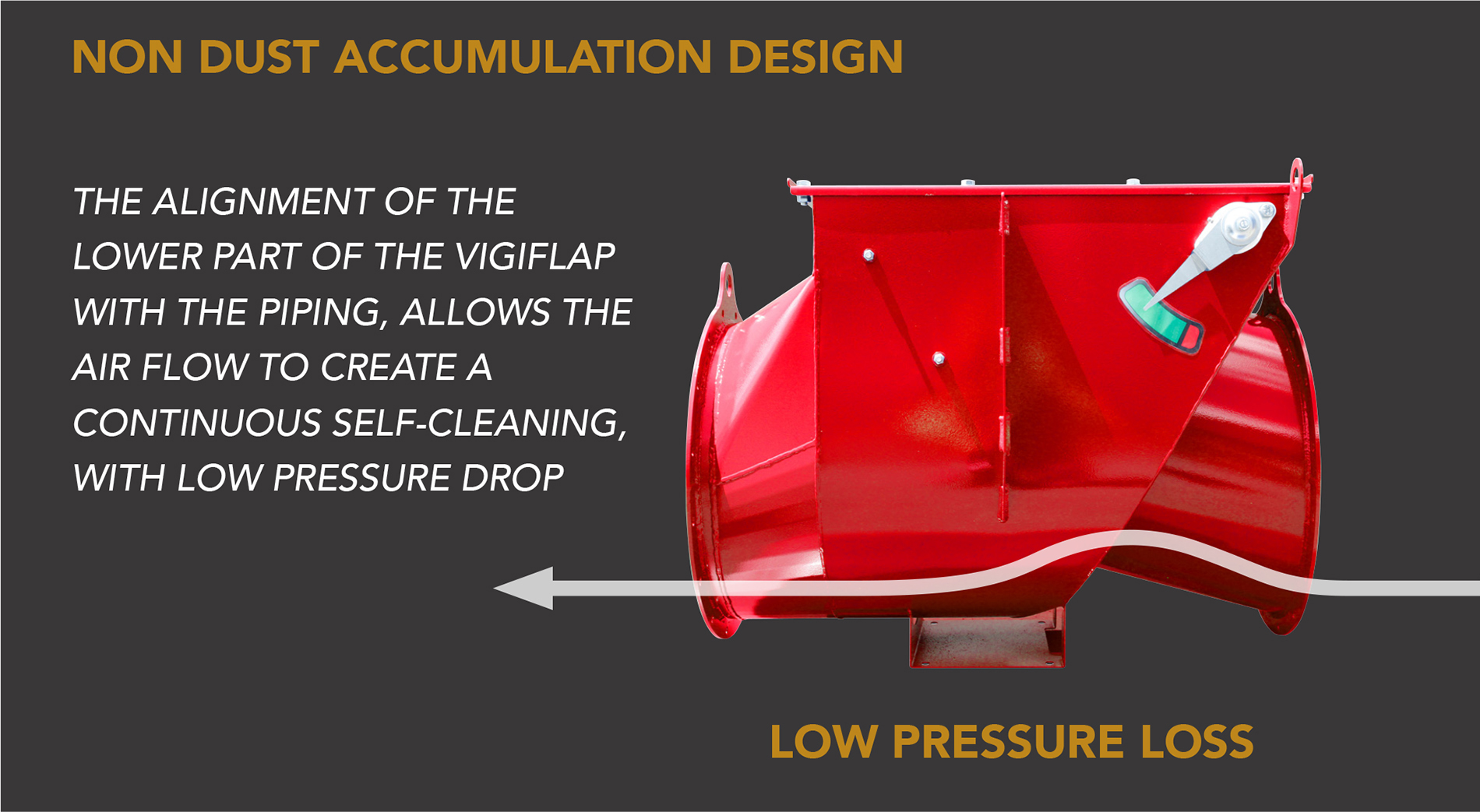
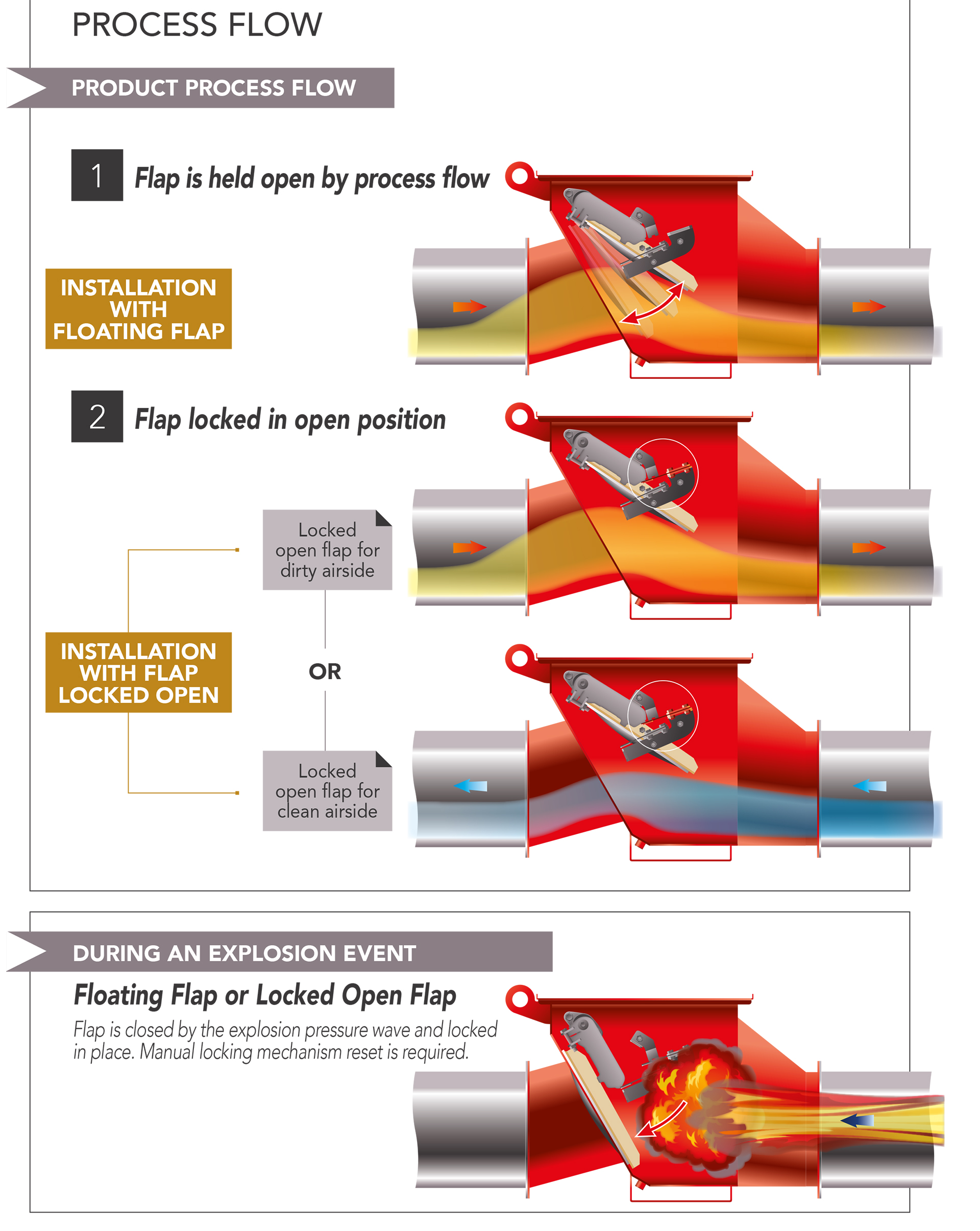
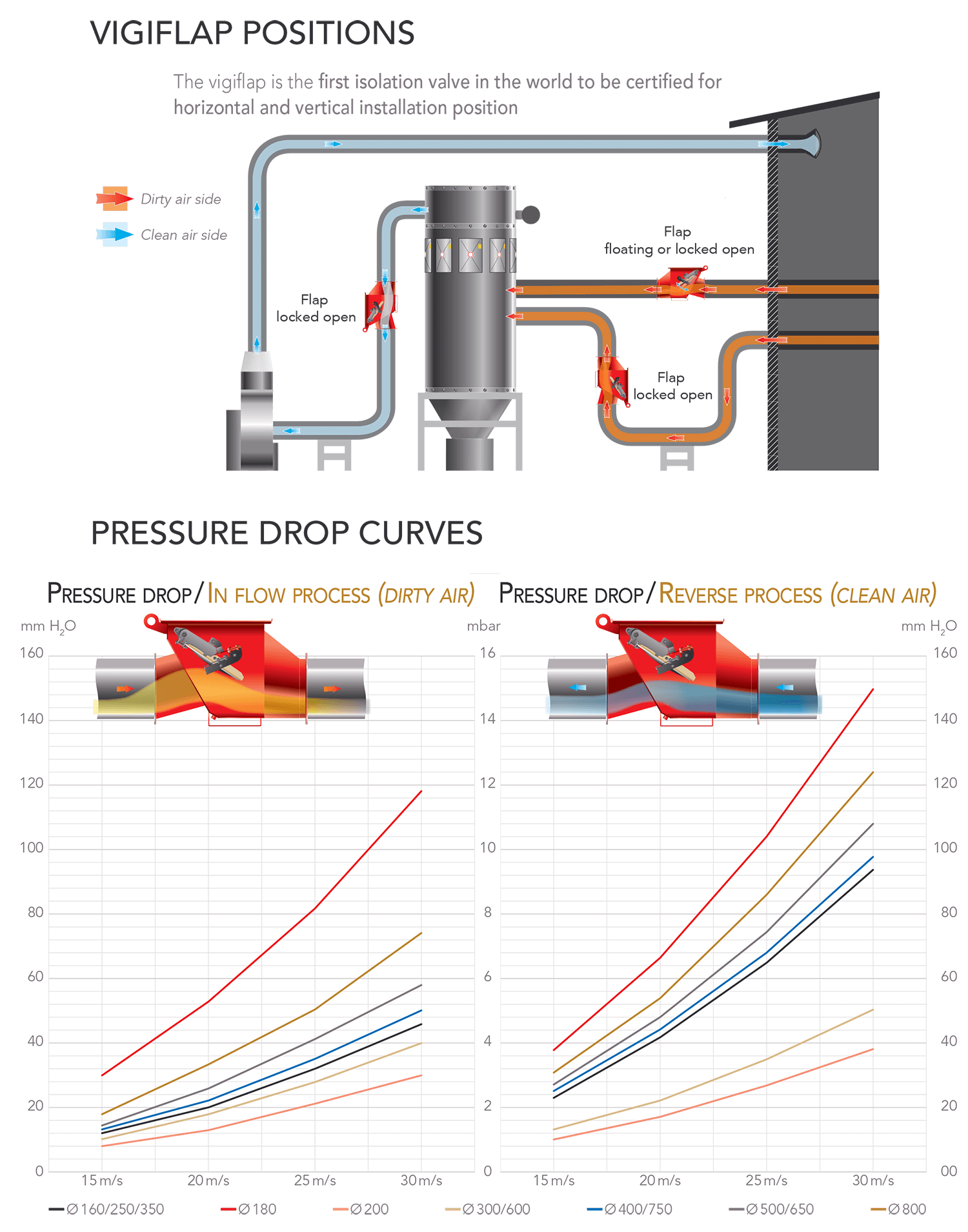